Please, insert Virtual Showroom access password:
A tried and tested
Work Process
A century of accumulated know-how enables us to anticipate problems and find the most innovative solutions. Rigorous quality control ensures a defect-free product
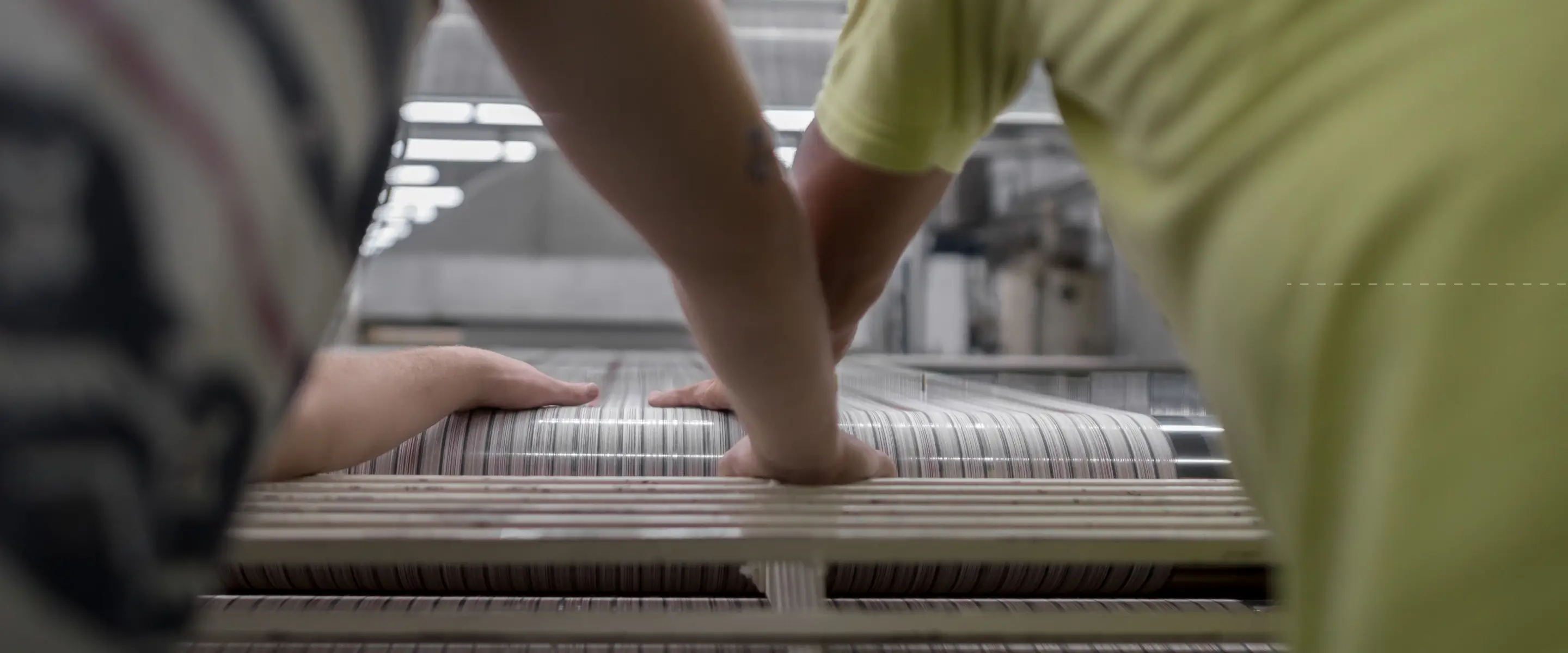
This is how
we do it!
We are a vertically company, which means we handle all production processes internally, thereby eliminating the need for subcontracting and dependence on external parties.
Quality Control
Throughout the production process, the article undergoes three phases of quality control inspection.
Planning
89,8% of orders are delivered within the agreed-upon deadlines. Only 2,5% of orders experience a delay exceeding one week
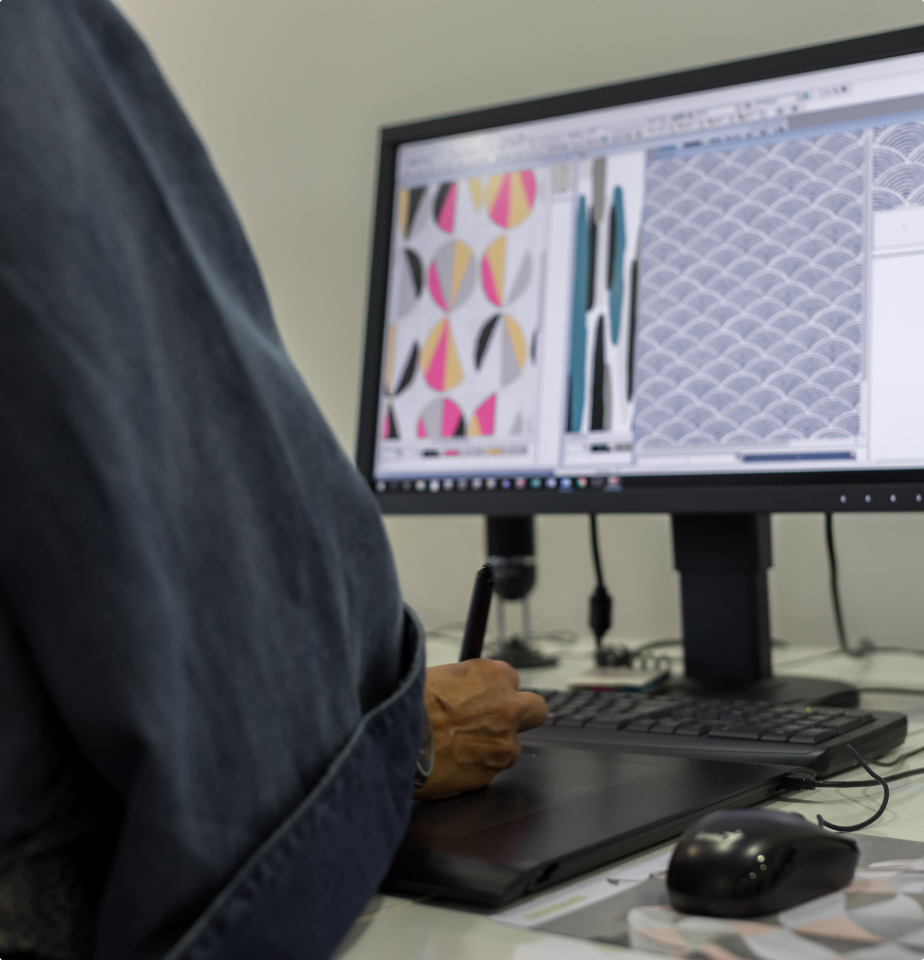
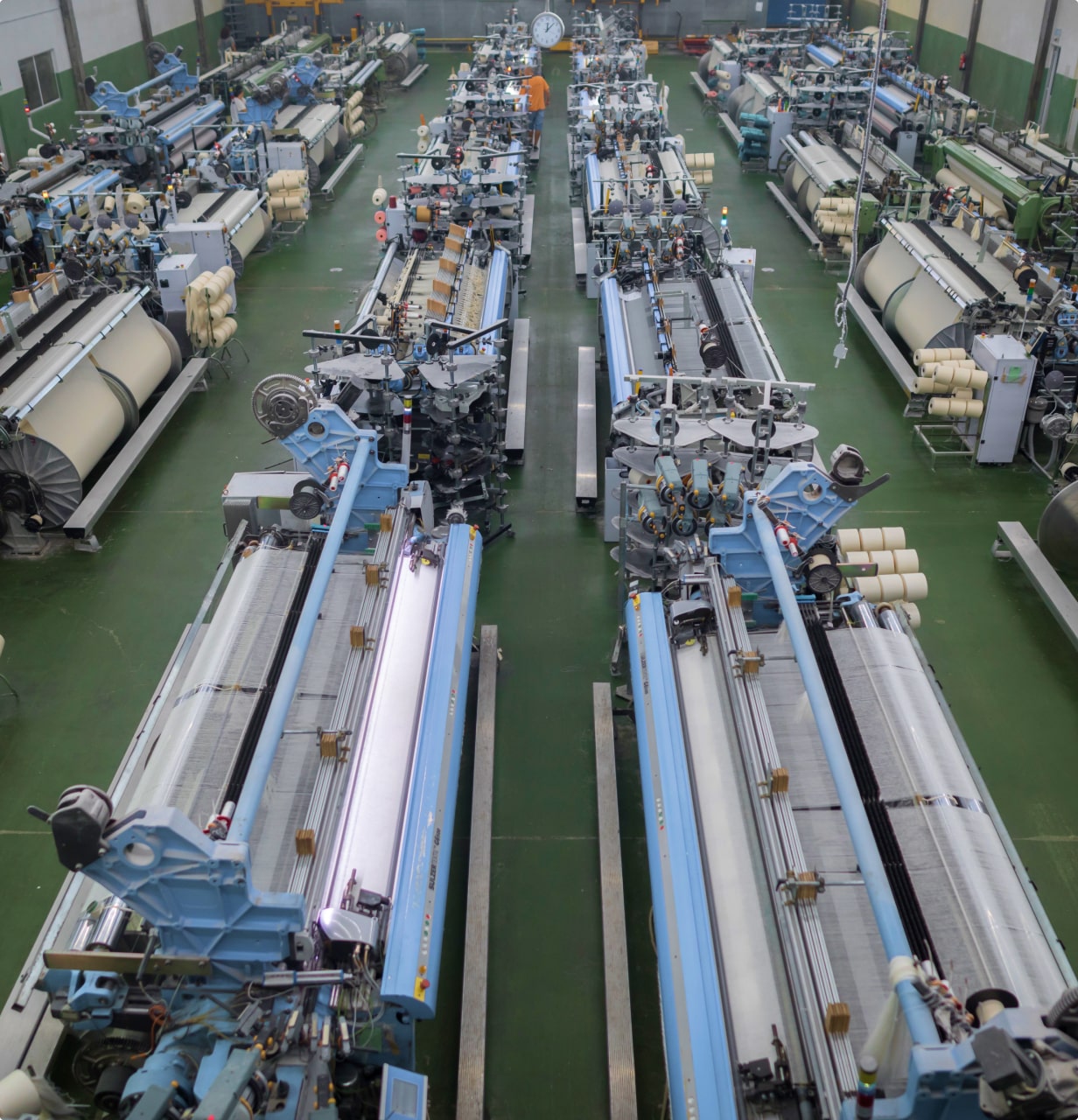
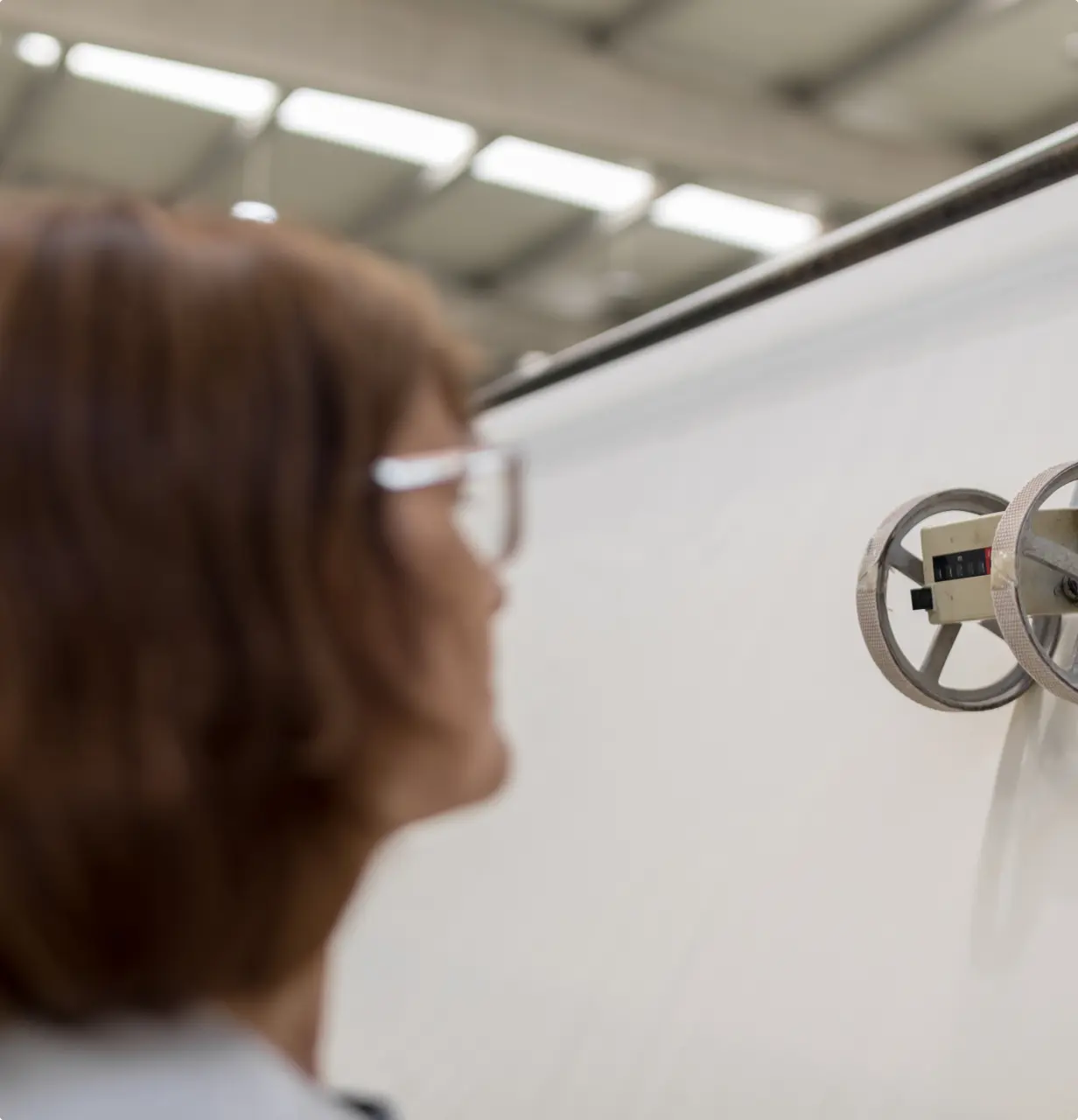
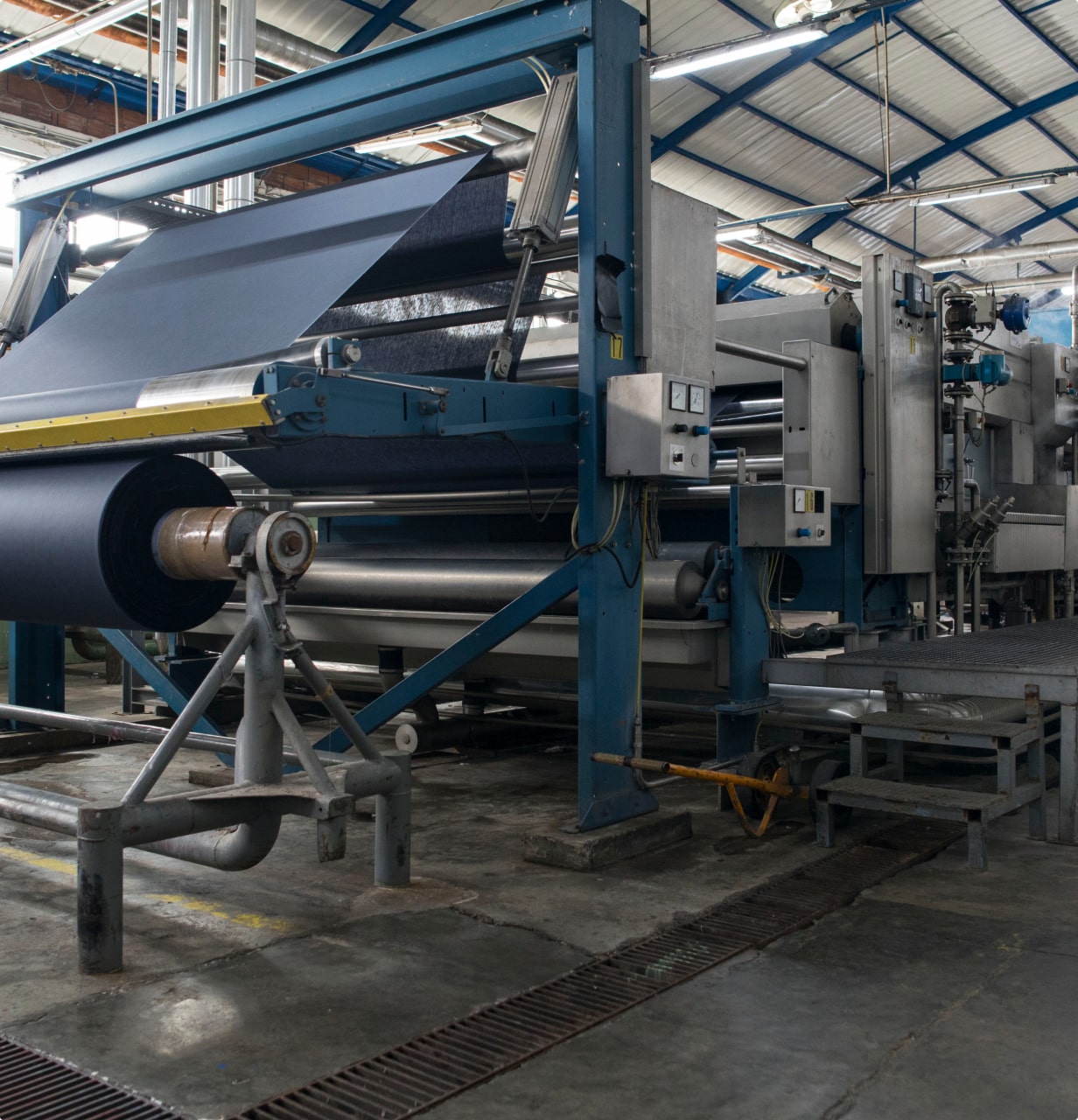
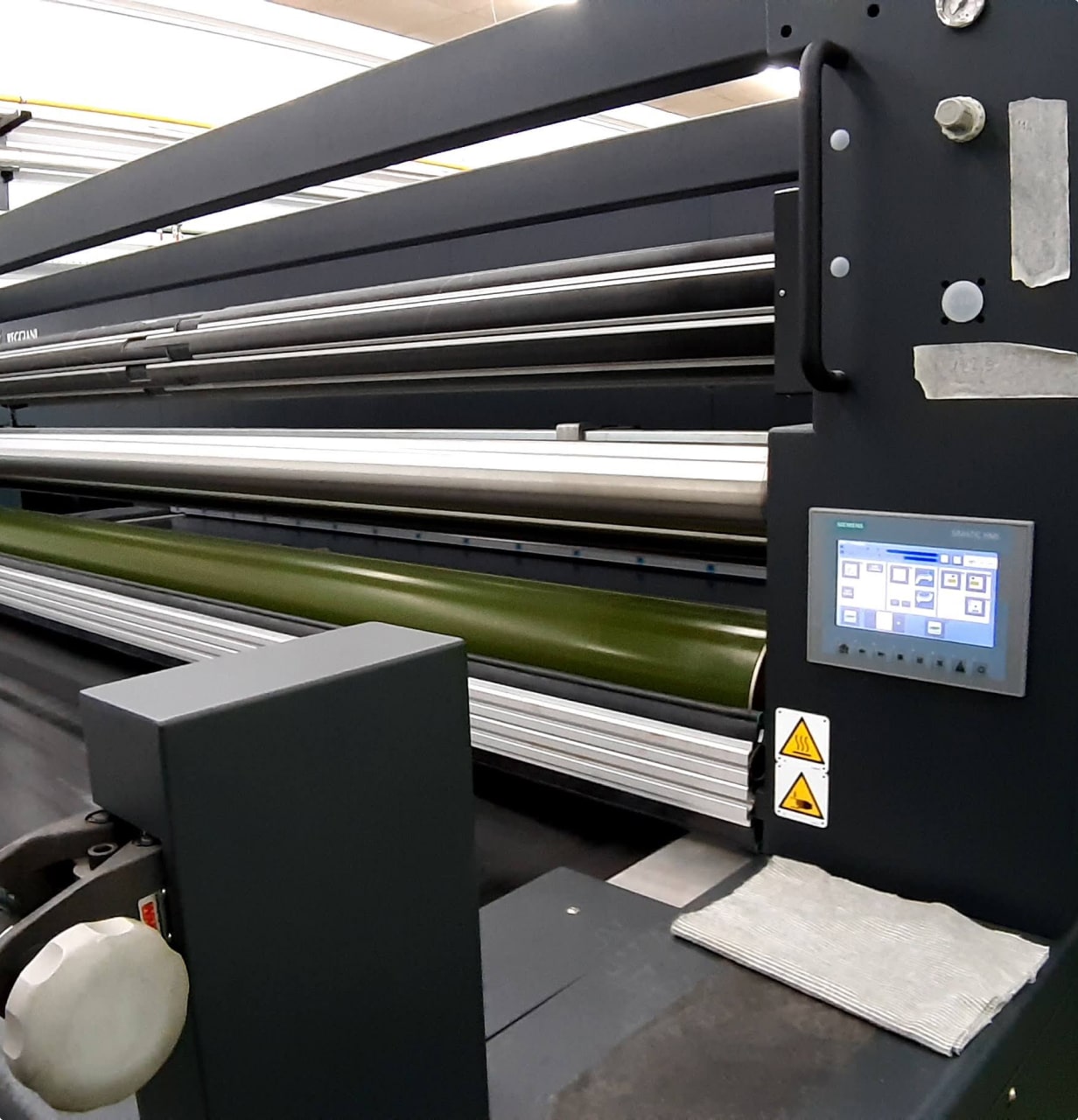
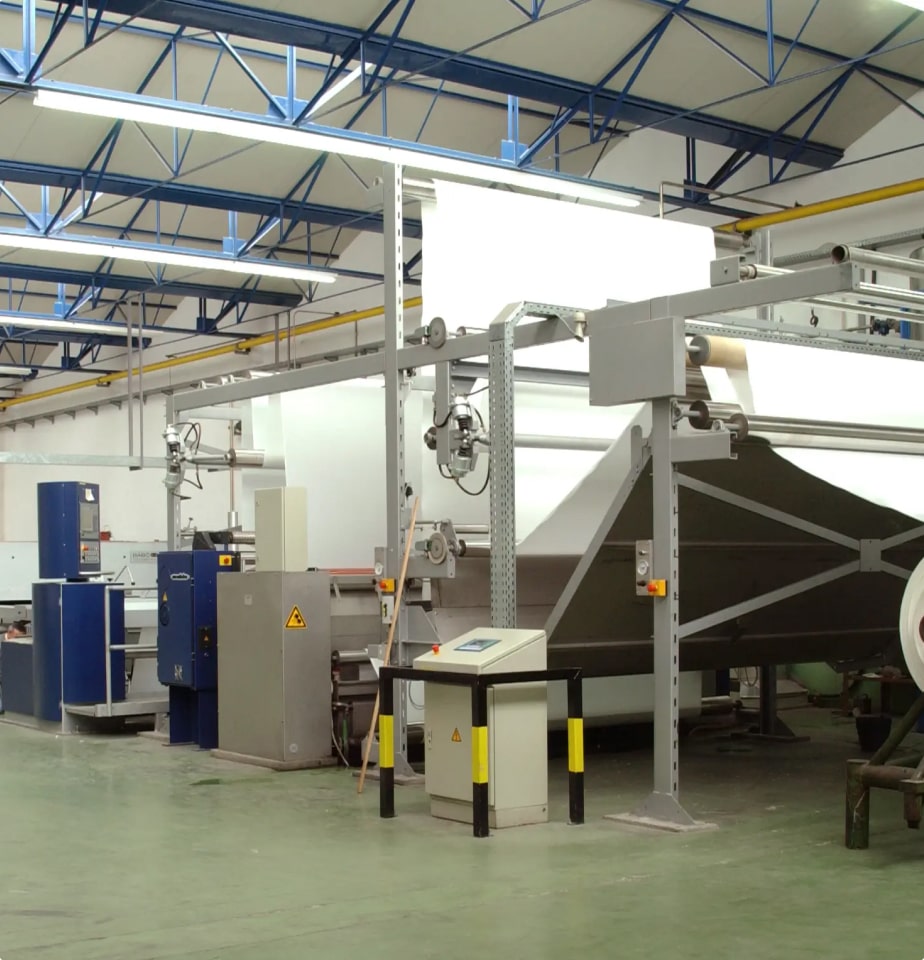
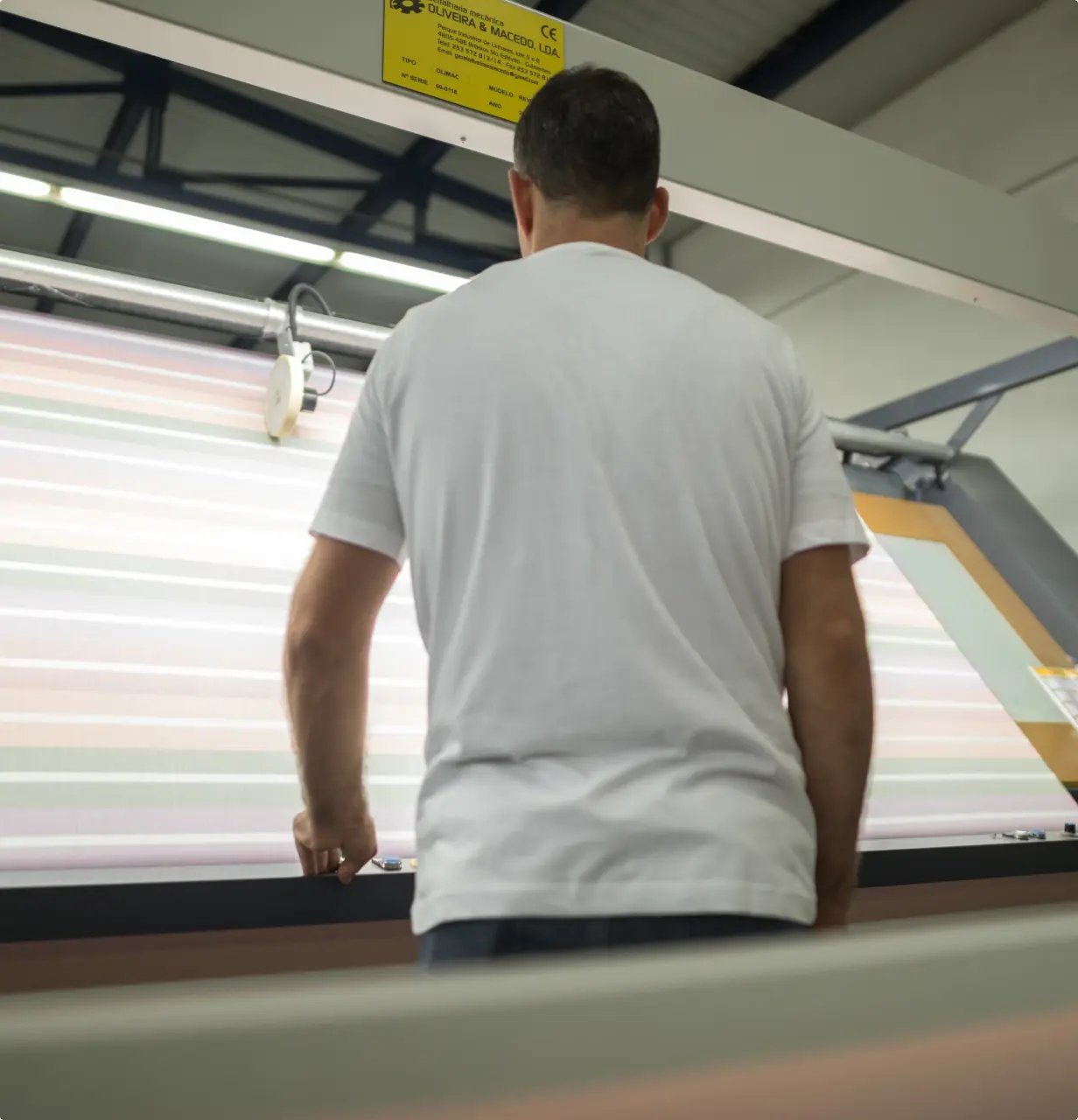
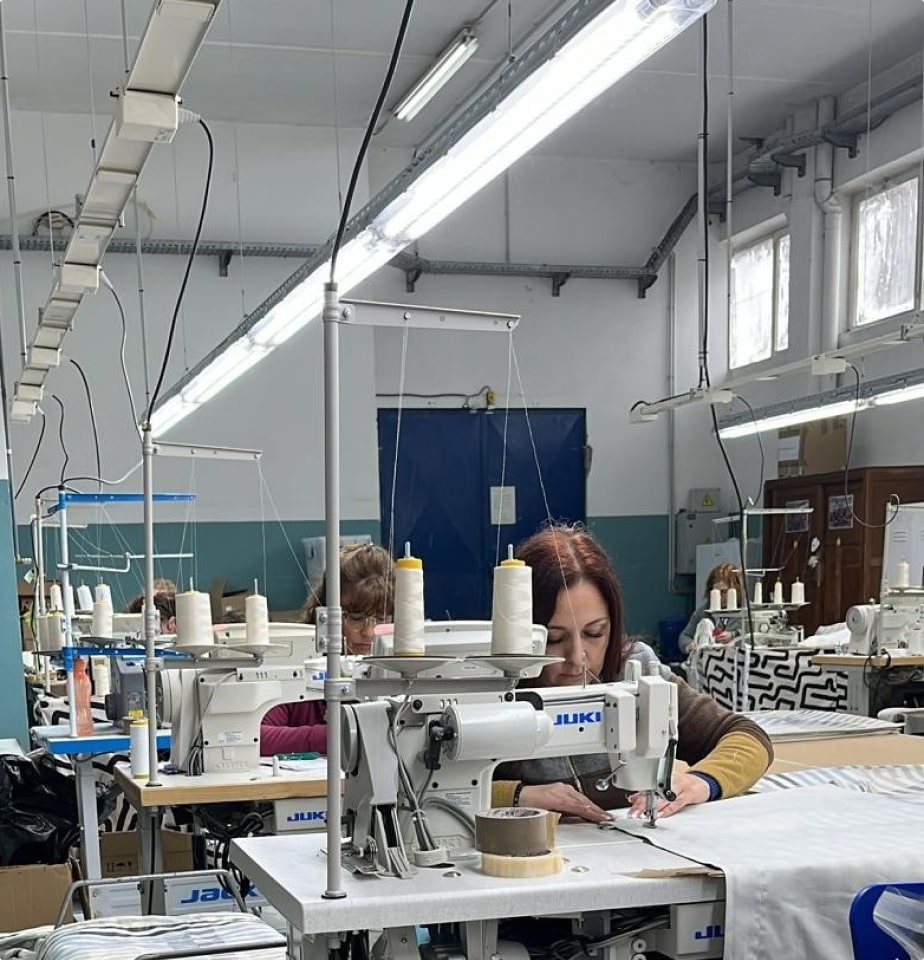
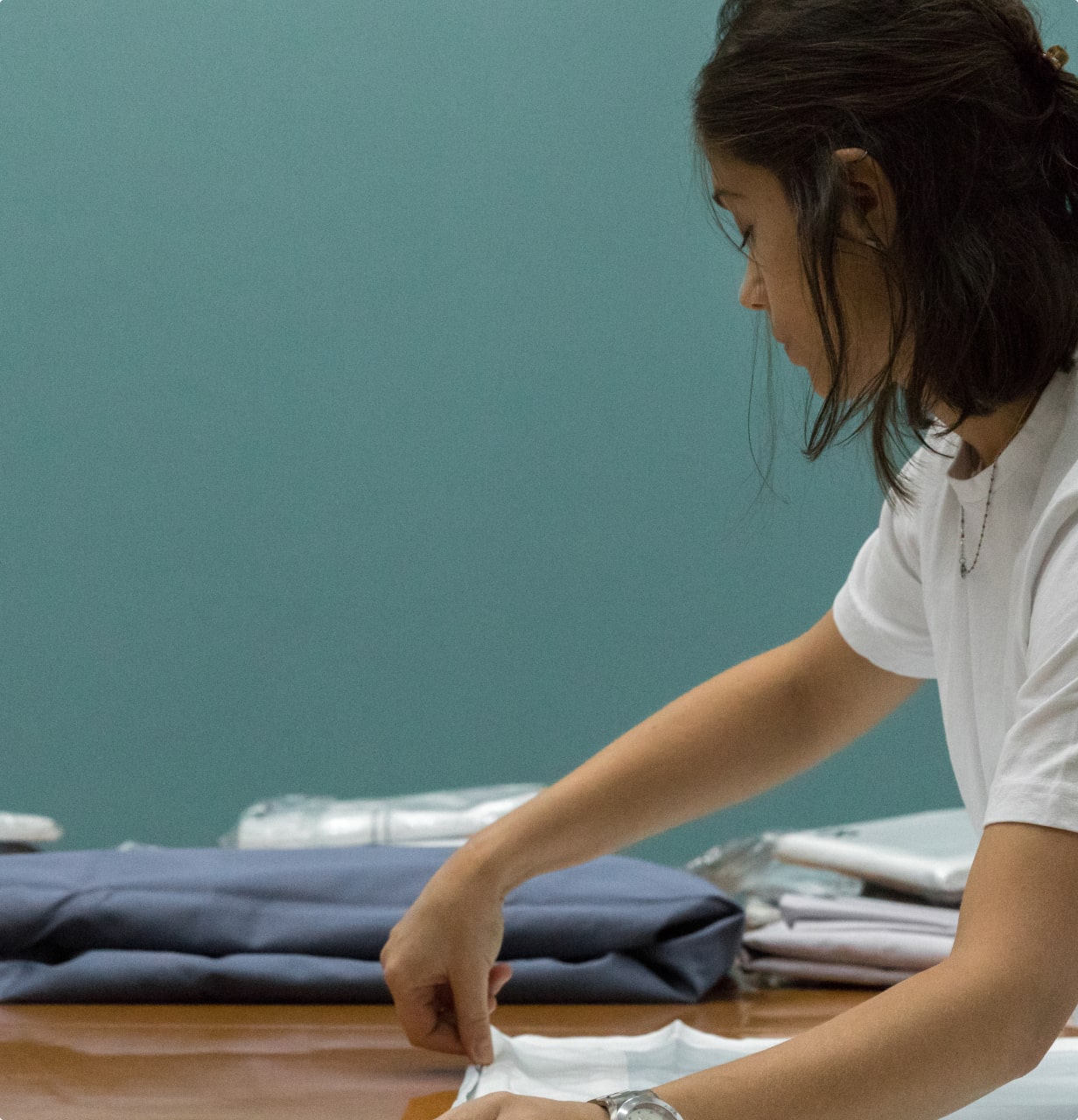
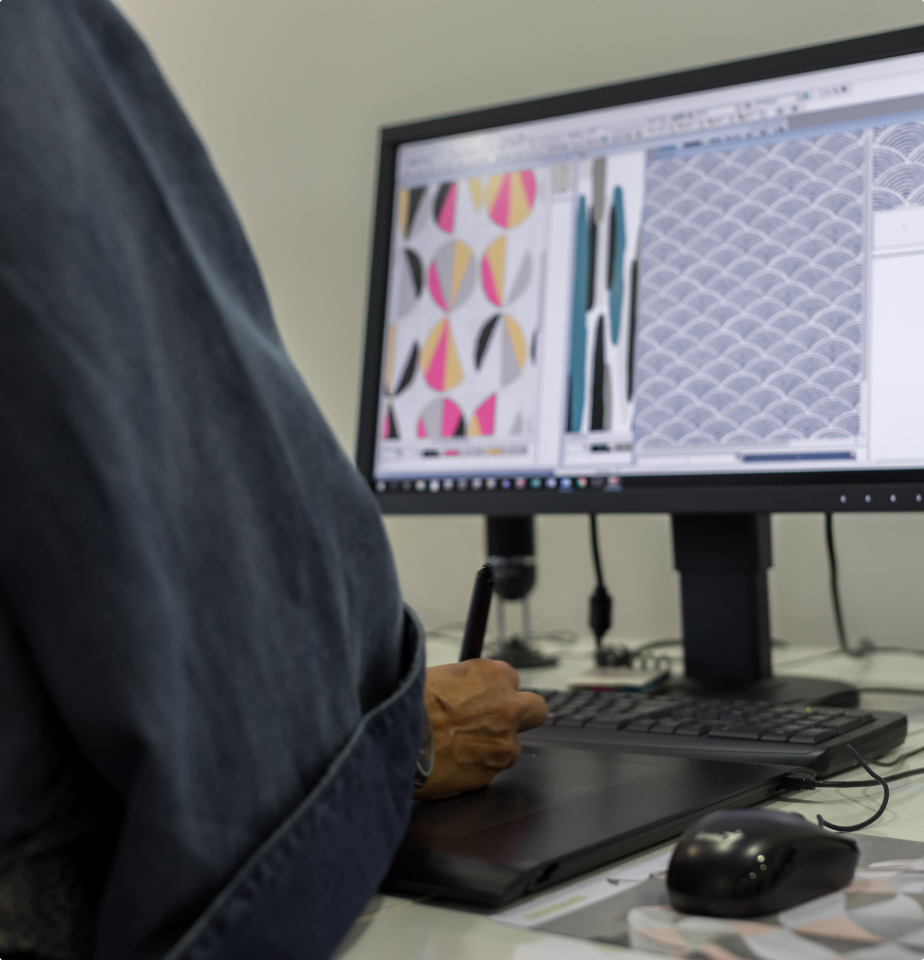
Step One
Design office
Our design team develops market trends! The creativity of our design team, combined with the most sophisticated creation software in the market, enables us to produce best-selling products every year. In addition to our own developments, we also bring our clients' ideas and designs to life.
For those with a specific color palette or an inspirational mood board, our designers can assist your team in developing suitable products that seamlessly complement an existing collection with harmony.
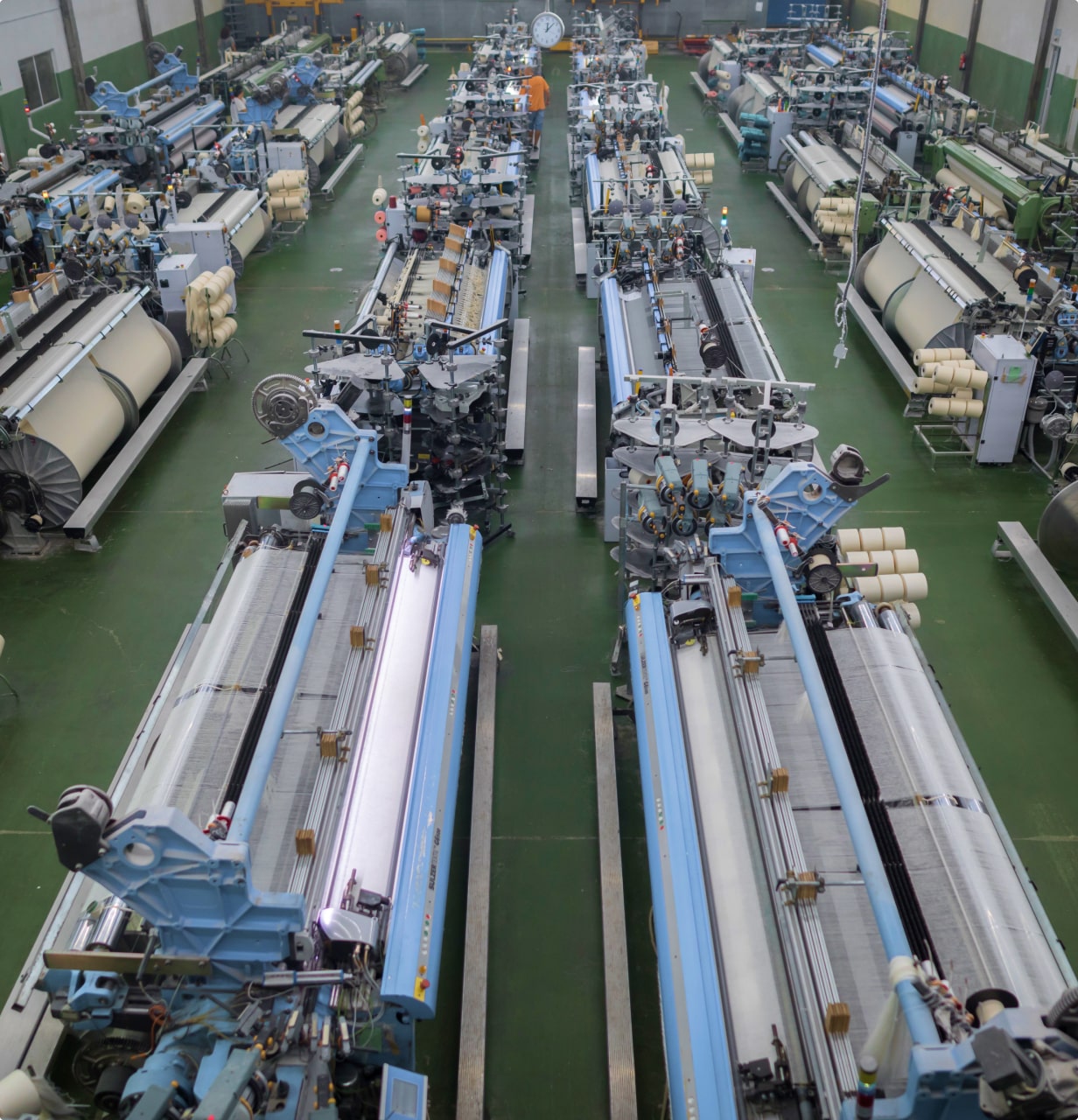
Step Two
Weaving
Weaving is the heart of our company. As we enter this section, it's impossible not to feel the frenetic heartbeat of our 60 looms, all controlled by a real-time production monitoring system and closely supervised by experienced weavers. Every year we produce around 548 tons of fabrics, which incorporate various raw materials, including natural fibers such as linen, cotton and hemp.
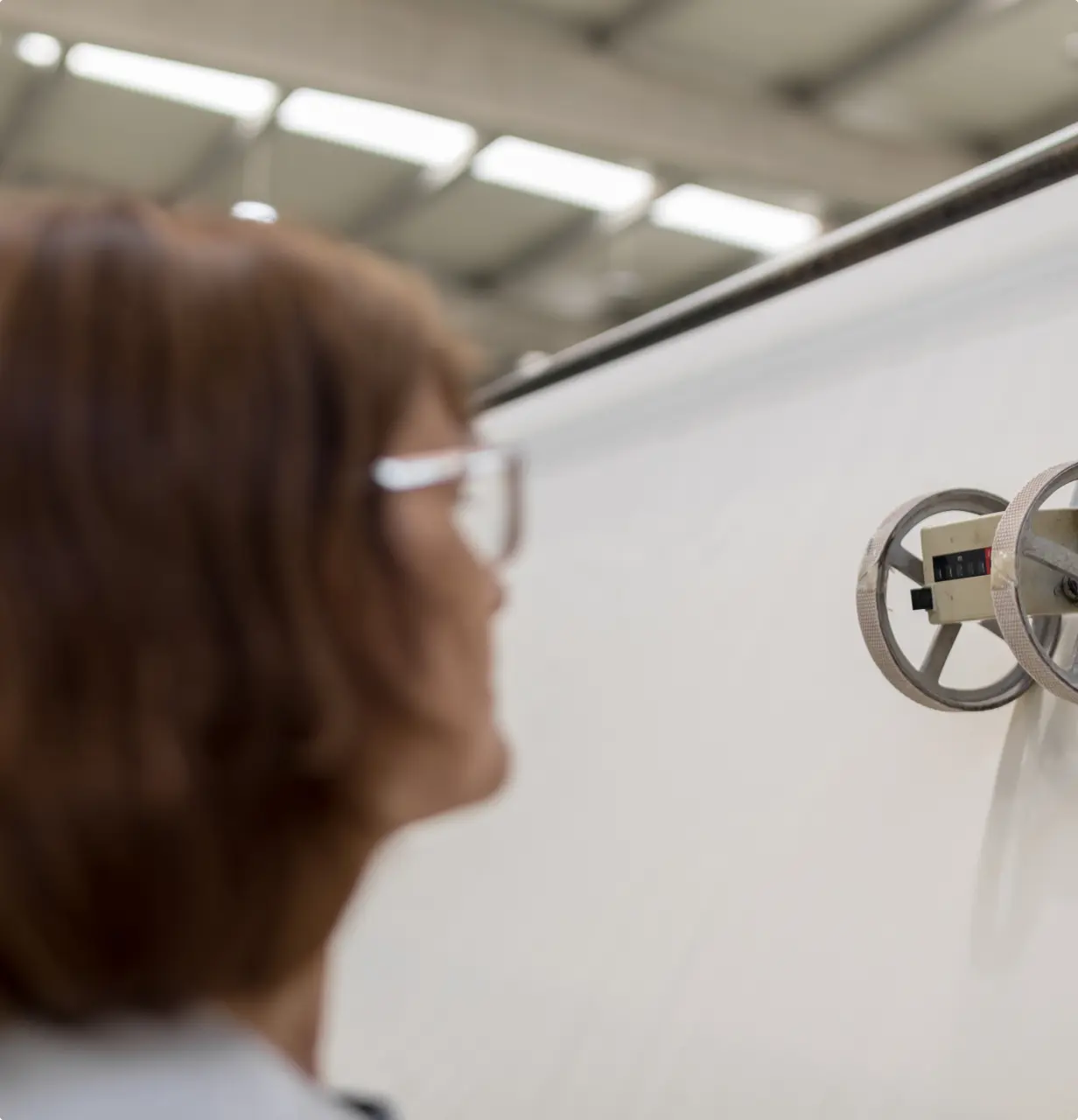
Step Three
Raw Inspection
This weaving support section allows the detection of defects at an early stage of the production process, enabling them to be corrected on the loom. At this stage, the verification is done manually, by specialized and trained employees.
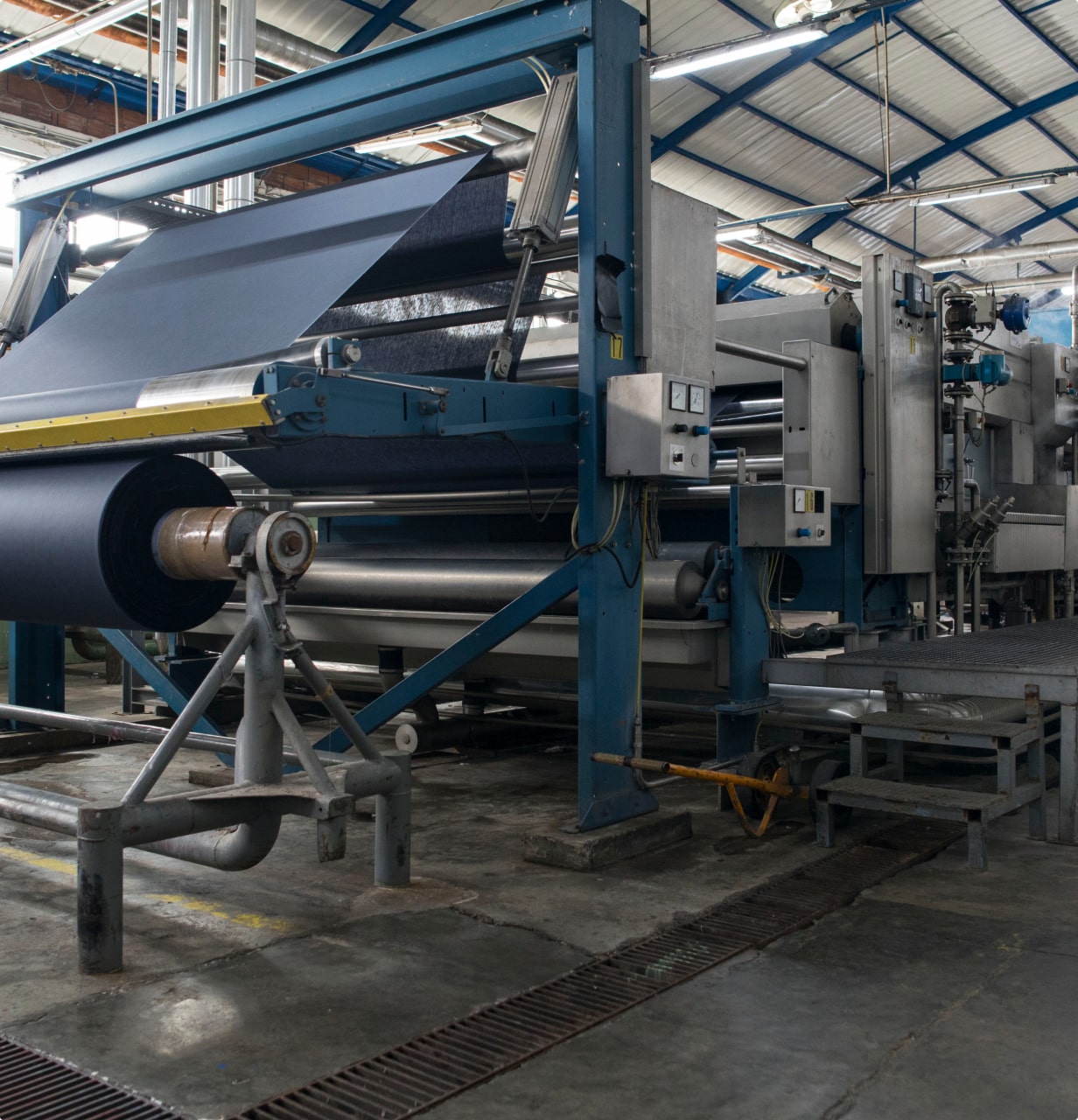
Step Four
Dyeing
Here we dye yarn or fabric, through a set of machines that allow various types of processes and operations, respecting the integrity of raw materials that are being processed, as well as the intended result of the client. All recipes that result in a specific color are recorded in a database, allowing for exact replication in case the customer submits a repeat order.
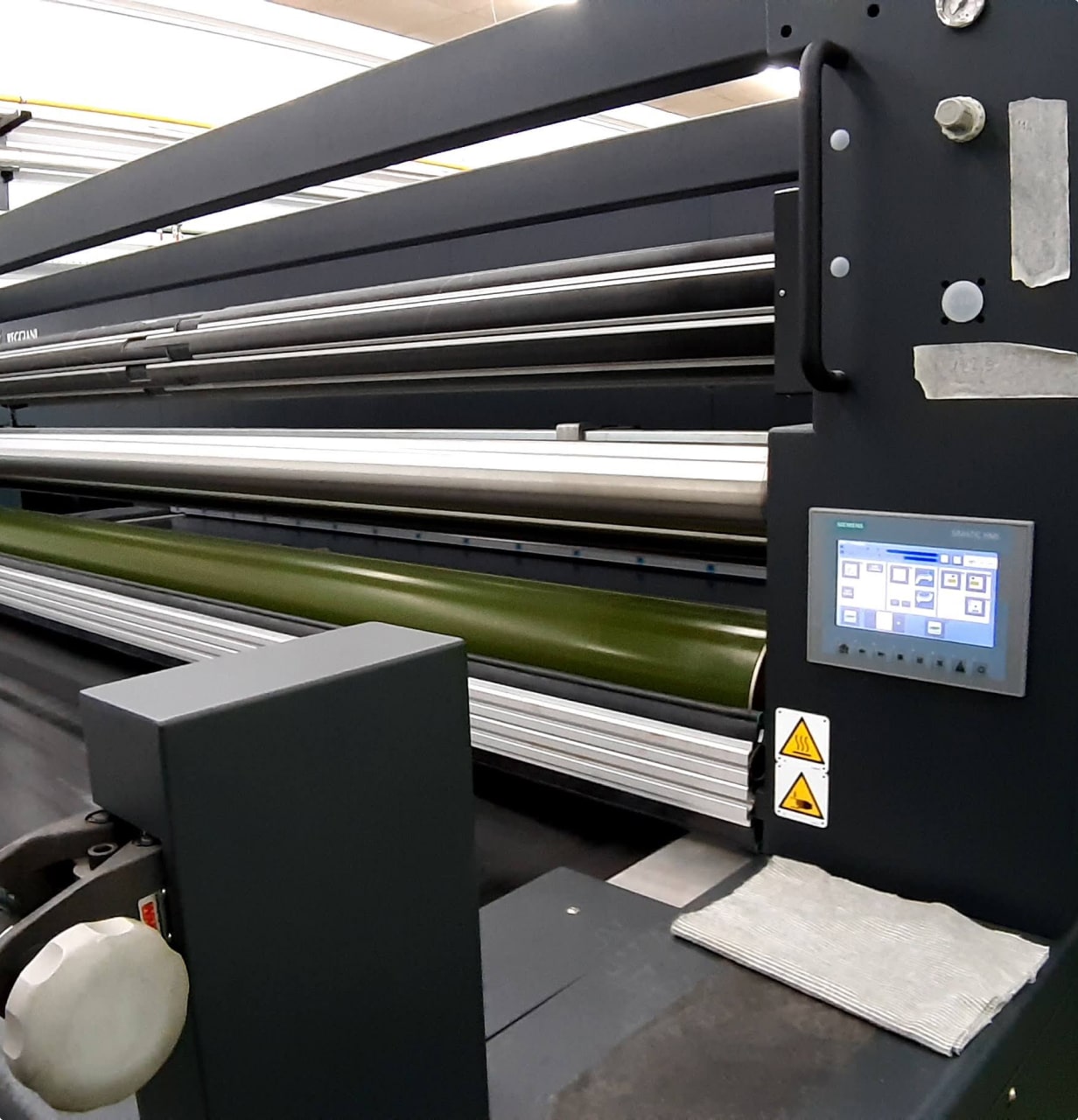
Step Five
Printing
Always with an eye on innovation, Sampedro recently invested in a state-of-the-art digital printing machine. This technology represents a game-changer in printing. Being a much more ecological it also overcomes any obstacles regarding colors and design rapport. With this machine we can now produce samples in a matter of minutes and without waste. We complement this section with a rotary printing machine, enabling higher production speeds and consequently, a more affordable price.
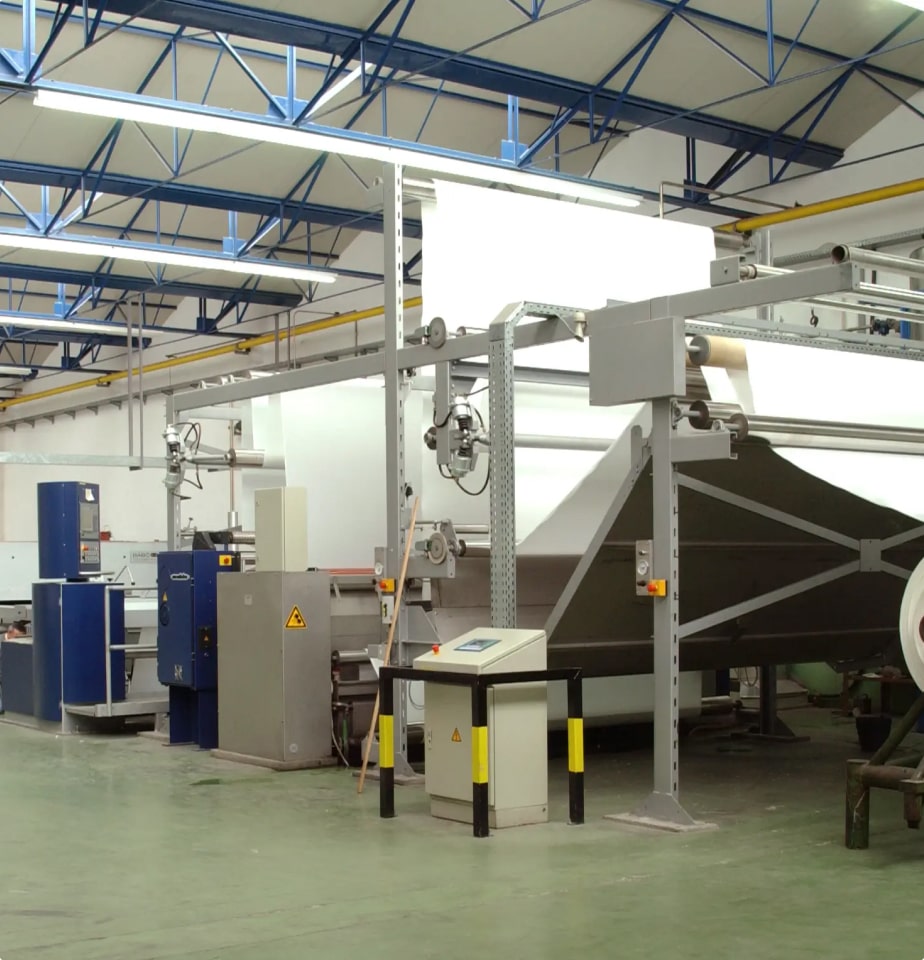
Step Six
Finishing
Why does our 200-thread-count percale have a better hand feel than another 200-thread-count percale? Largely due to our finishing section! This is where we give the fabric its final touch, utilizing both chemical and mechanical treatments we apply some common treatments in this area as well as some secret formulas developed in-house!At this stage of the production process, we have a variety of machines that enable us to manipulate the final texture of the fabric according to the parameters desired by each customer.
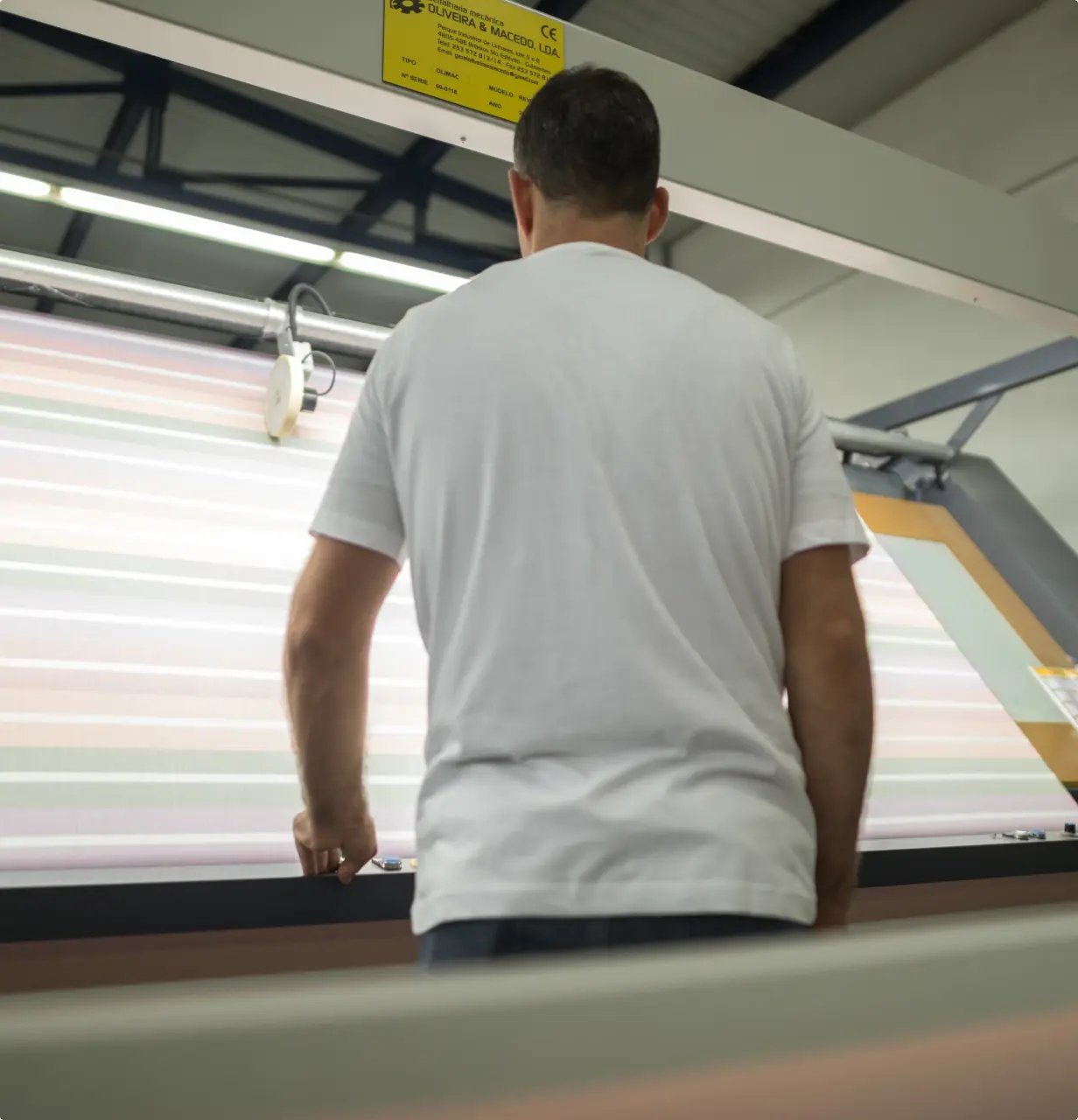
Step Seven
Final inspection
After all the processes described above, the fabric is ready to be manufactured, but not before it has passed through the watchful eyes of our inspectors. Here, 100% of the fabric is inspected to identify and mark any production defects. Although we can't correct these defects at this stage, we can at least mark and remove them to ensure they don't reach the end customer!
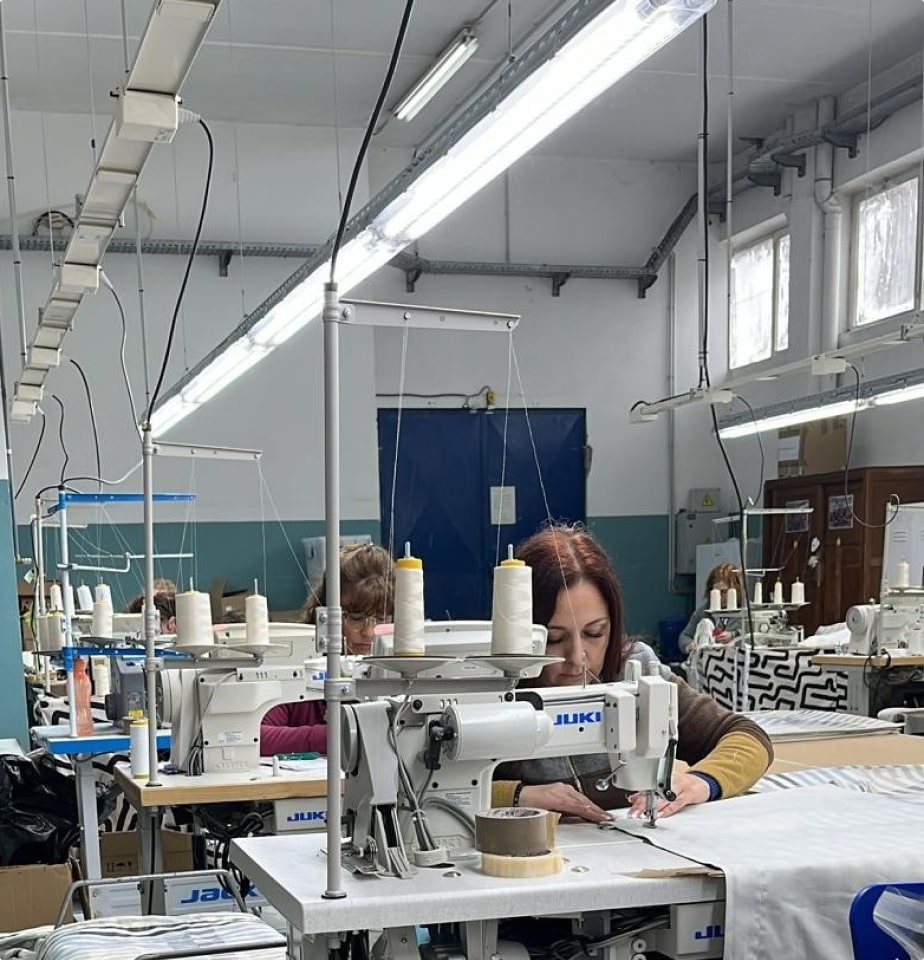
Step Eight
Cut and sewing
In this section, automatic machines cut the fabric with millimeter precision. The skilled hands of our talented seamstresses shape a wide variety of garments according to each customer's requirements.
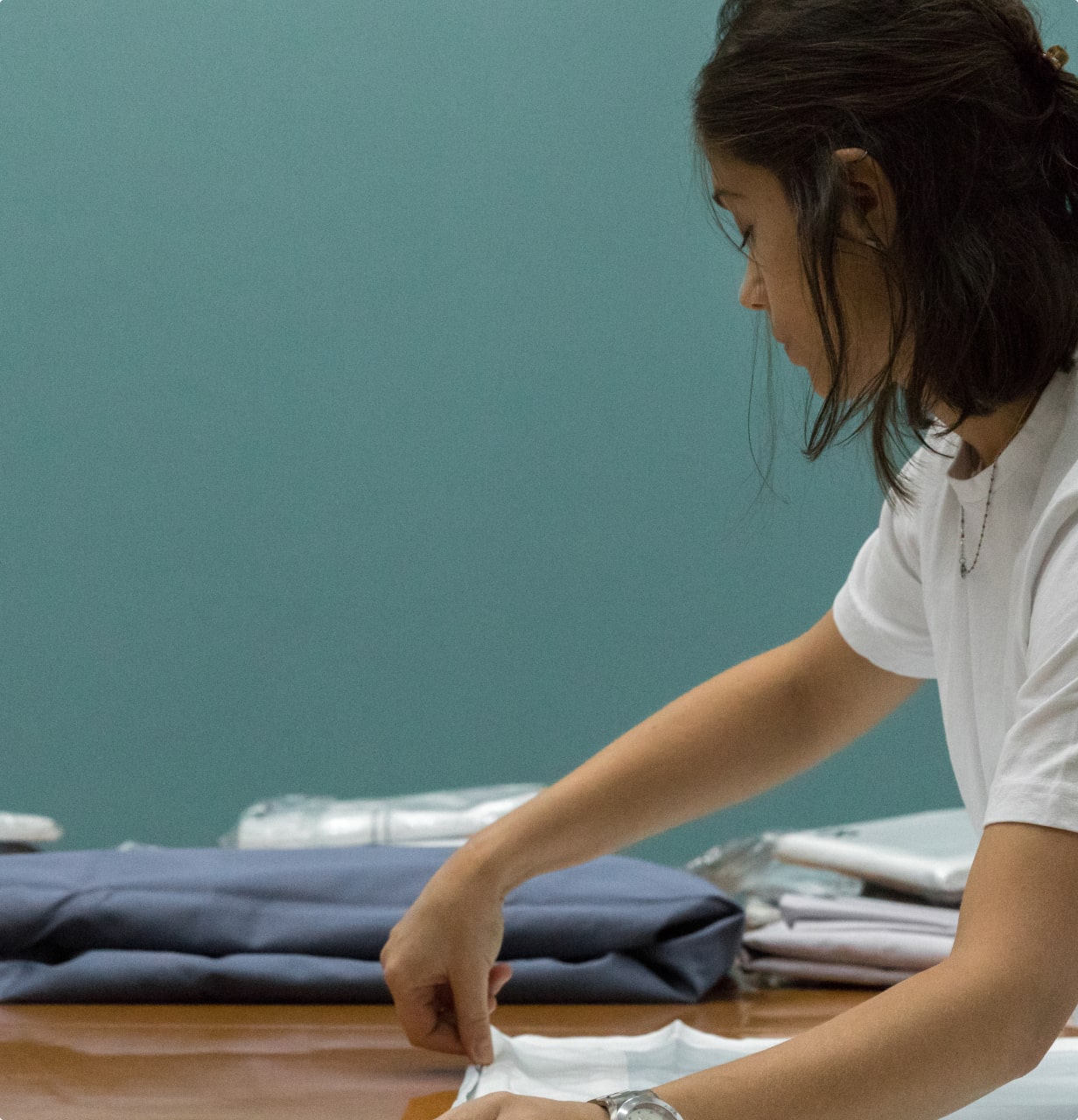
Final Step
Final check
Before packaging, the pieces undergo another rigorous quality control check to ensure they match the previously approved standard piece. Packaging , Barcodes , Inlays , Labels and other accessories are checked by more than one person before the pieces are made available to our dispatch warehouse, from where they will be shipped.
Frequently Asked Questions
In this section, you will find answers to the most frequently asked questions. However, please do not hesitate to contact our sales team for any further clarification.
What are your Minimum Order Quantities (MOQs)?
We tailor our production to meet the individual requirements of our clients, producing per order. Our MOQs typically start at 1000 meters per fabric, which can be divided into 500 meters across different colorways and can also be further divided to accommodate all your sizes and SKU´s. 500mts is approximately 120 Duvet Covers per color.
What certifications do you have?
Our company holds certifications including ISO 9001, OEKO TEX CLASS1, GOTS, BCI, and CEDEX.
Where do your linen yarns originate from?
Our linen yarns are sourced from European Flax, predominantly from Belgium and France.
Do you work with Organic Cotton?
Yes, we do. Upon request, we can accommodate the use of organic cotton in our production.
What is your process for samples?
We can provide swatches of different materials upon request, and we also send a pre-production sample before commencing full-scale production.
Customer Testimonials
Clients who experienced the Legacy of Portugal's Oldest Textile Factory
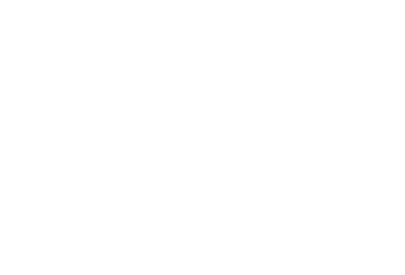
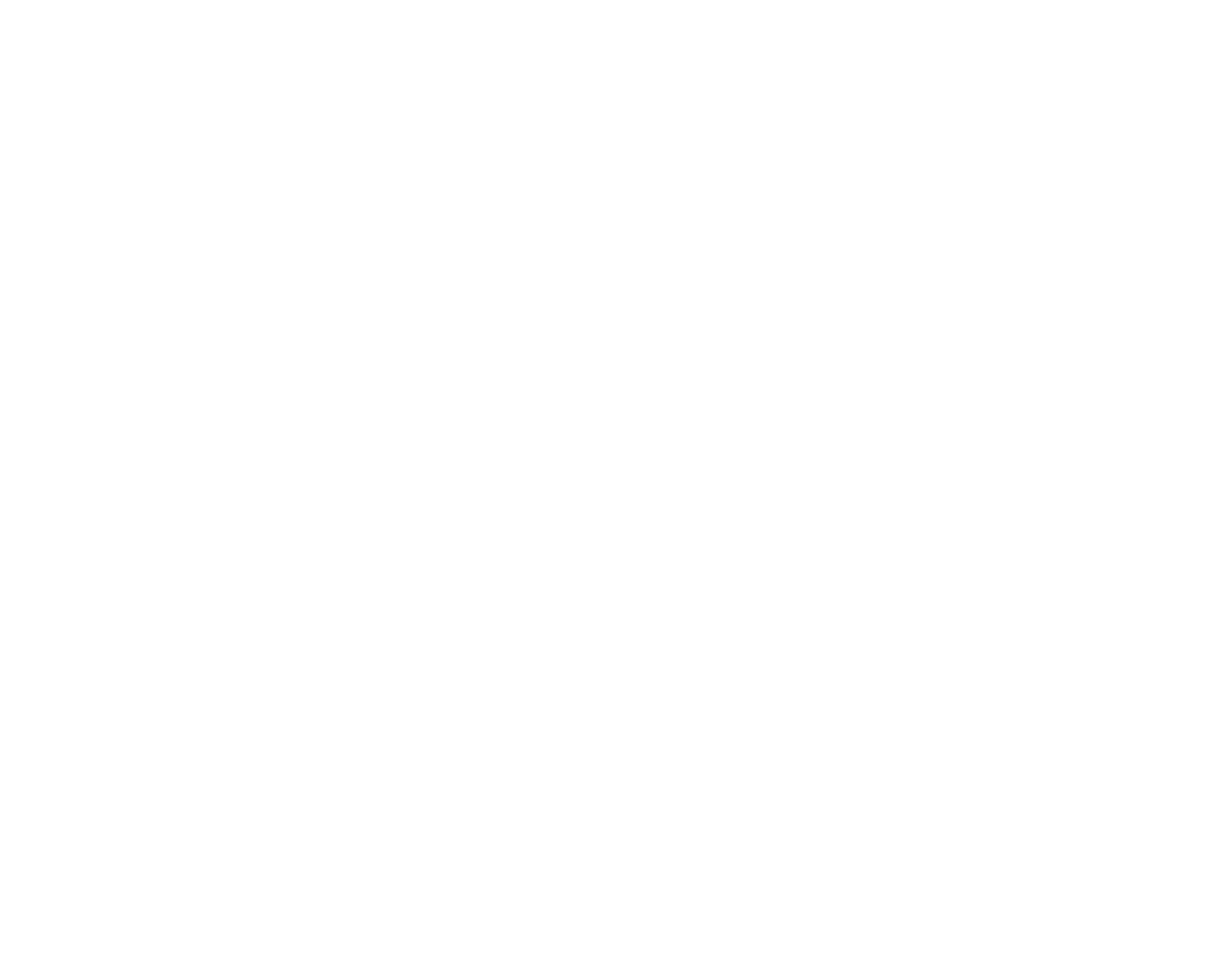